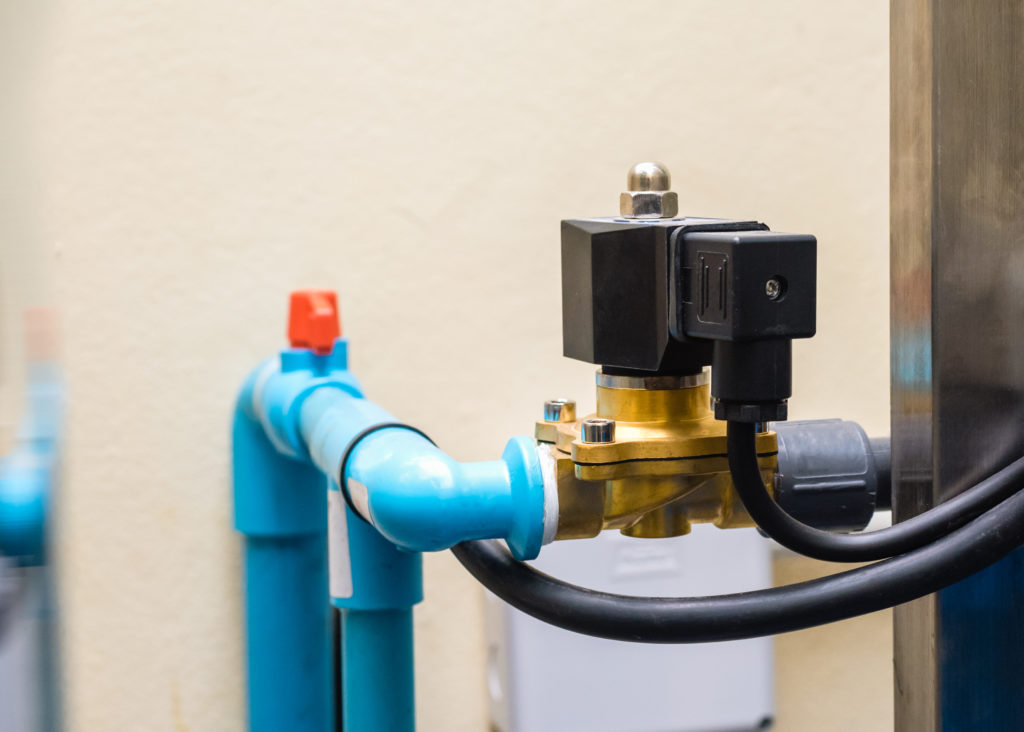
There are certain industries wherein the demand for smaller, more accurate, and higher-performing instruments is constantly growing. For instance, there are many applications in the medical industry that require extreme levels of performance. It can be analytical chemistry (mass spectrometry and gas chromatography) or medical devices (laser therapy and hemodialysis).
This increasing demand for sophisticated instruments has highlighted the importance of solenoid valves. These valves offer precision control in gas and liquid handling applications. That is why they are being used in various industries. They are also being manufactured in a wide range and each one employs a different mechanism to control the media.
Solenoid Valve Market
Image Source: https://dataintelo.com/report/solenoid-valves-market/
The global market for solenoid valves was valued at nearly USD 4 billion in 2019. It is estimated it will increase at a CAGR of around 4% and surpass USD 5 billion by 2026 during the forecast period.
This rapid growth is projected because these valves are being increasingly used in several major end-user industries such as oil and gas, automotive, food and beverages, and the utility sector. These industries prefer solenoid valves as automatic valves because of their high efficiency, ease of use, and relatively low prices. So, they are turning out to be a reliable, efficient, and innovative component to meet the needs of new, demanding applications.
How to Choose the Right Valve for Extreme Levels of Performance
A typical solenoid valve is selected for an application based on four key factors. These are:
- The pressure going into the valve,
- The type and state of the fluid,
- The size of the pipe connections to the valve, and
- The voltage
Depending on these four requirements, you can pick the right kind of valve for the job. However, when these valves have to be used in applications requiring extreme levels of performance, some other capabilities are considered as well. Take a look at some of these factors:
1. Low Leak Rate
There are certain applications where fluids have to be sophisticatedly controlled and you cannot afford even a small leak. For instance, a tiny leak can result in inaccuracies in analytical chemistry applications.
However, a very low level of leak rate in most valves can be quite challenging. This is where solenoid valves come in. They allow instrument manufacturers to simplify any design because they reduce the need for secondary positive shut-off valves. And, it helps in achieving a very low level of leak rate.
2. High Temperature
A “T-code,” or temperature code helps in identifying the maximum surface temperature that a component can reach in given conditions. Some process industries like oil and gas, chemicals, and power generation are placed in hazardous locations. Even a small explosion there could cause extreme damage and personal injury or loss of life.
That is why it is important to check for the maximum ambient temperature rating before choosing the right valve. You can look for the stated requirement and select your valve according to the lower maximum ambient temperature listed on its label.
3. High Pressure
There are some applications that demand a high pneumatic pressure capability. In such cases, you can pick a valve with an orifice rated up to 86 bar (1,250 psi). It allows manufacturers to replace expensive hydraulic valves with them and save money.
4. Fast Response Time
The performance of solenoid valves determines the performance and safety of the pneumatic system to a large extent. It makes the response time and maximum action frequency of the valves an important consideration in high-precision and high-speed pneumatic systems. A typical strong solenoid can offer a fast response time of <5msec that works ideally in most situations that require extreme performance.
Image Source: https://www.betavalve.com/Wiki/72/Valve-Response-Time
When deciding on the response time, you need to consider the type of valve, the nature of the media, the pressure, and the current (AC or DC). A faster response time is extremely useful in applications where timing is used to estimate the volume of fluid being used in the application. Any potential long response times in such situations can compromise the accuracy of the volume of fluid being dispensed.
Solenoid valves are increasingly becoming important in today’s delicate applications. You will find them commonly in use in automated manufacturing systems, automobiles, refrigeration, and AC systems. However, they are also capable of being used in applications that require extreme levels of performance.